System Curves
Tutorial
The total head at any given flow rate consists of two parts: static head and frictional head. The frictional head loss consists of major losses (piping) and minor head losses (component losses). Each of these is described in further detail below. A system curve shows the total system head required over a range of flow rates.
Pressure and Head Relationship
Head is the expression of the energy content of a liquid in reference to any arbitrary datum. It is expressed in units of energy per unit weight of liquid. The measuring unit for head is feet of liquid.
Pressure and head of a liquid have a physical relationship as outlined in equation 1.A.1. These equations utilize a conversion constant and specific gravity (s), which is defined in equation 1.A.2. It is common to use head because the performance of the pump can be shown independent of the specific gravity or density of the fluid pumped.
where:
- H = head in feet (ft)
- p = pressure in pounds per square inch (psi)
- s = specific gravity (unitless), see equation 1.A.2
Specific gravity (s) is calculated by equation 1.A.2 and values of specific gravity for water and other liquids can be found in the fluid properties section.
where:
- ρ = density, typically in lbm/ft3
Static Head
Static head consists of both the elevation and pressure difference between the supply and destination of the system. This typically does not depend on velocity and is therefore constant for the system curve. This can be calculated using equation 1.A.3.
where:
- Δhstat is differential static head, feet
- z is elevation, in feet (ft)
- p is pressure, in psi
- ρ is fluid density, in lbm/ft3
- 144 is to convert between square inches (in2) and square feet (ft2)
Note: Acceleration due to gravity is omitted in Eq. 1.A.3 due to units; therefore, it is only valid for standard earth acceleration due to gravity.
This equation is based on the supply and destination being tanks or where the velocity of the fluid can be considered zero. If the pressure measurements are taken with a gage where the velocity is not negligible then the velocity pressure (or dynamic pressure) must be added to the pressure gage reading as indicated in equation 1.A.4.
where:
- pgauge is pressure measurement at the gage, in psi
- ρ is fluid density, in lbm/ft3
- v is fluid velocity, in ft/s
- Q is volumetric flow rate, in ft3/s
- A is pipe cross sectional area, in ft2
- 144 is to convert between square inches (in2) and square feet (ft2)
- 32.2 is to convert mass to force
Since the velocity will be different for two gage measurements in different pipe diameters, each of the pressures should be converted separately based on the conditions at the gage before using them in equation 1.A.3. Therefore, the pressure at the supply and destination can be defined as detailed in equations 1.A.5 and 1.A.6.
Note that if the supply and destination boundaries are at the same pressure, as is the case with open tanks, then the static head is simply the difference in the liquid elevation.
For the following discussion, it is assumed that the supply and destination tanks have negligible velocity (tank levels are constant or change very slowly).
Frictional Head
The head loss due to friction will vary based on flow rate (velocity) and can be calculated for the system components, such as piping, valves, elbows and bends, and end-use equipment, etc. These losses typically vary proportionally to the square of the velocity.
Major Losses
Frictional head losses in pipes can be calculated using the Darcy-Weisbach equation. The Darcy-Weisbach friction factor, f, can be determined using the Colebrook-White equation (defined in Fluid Flow – General).
These equations will approximate the Moody diagram. The friction factor is based on the Reynolds Number (Re), the pipe diameter (D), and the pipe roughness (ε). The pipe roughness is dependent on the type of pipe. Other aspects, such as age, fouling, and coatings will also affect the pipe roughness. An example table of typical values for steel pipe materials can be found here. For other pipe materials, see section IV.
The Hazen-Williams equation is another method to determine pipe losses. These values are only valid for water at standard temperature. The Hazen-Williams C-Factor is a function of pipe material only and is not dependent on Reynolds Number.
Minor Losses
Minor losses in a piping system occur when fluid passes through a fitting, valve, area change, or enters or exits a tank, etc. Any system component that obstructs or changes the direction or pressure of the flow can be considered a minor loss. These are categorized differently than the pipe frictional loss (or major loss). In some systems, these minor losses can be the dominant system loss.
The loss created by the component is often characterized by a constant, K, and tabulated for several types of components. Head loss is determined by the equation defined in Fluid Flow – General (K values are also tabulated here).
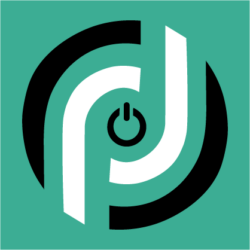
System Hydraulics: Pump & System Curves, Control & Energy – On-Demand Training
Learn the components of the system curve and how to calculate it, the pump curve, determination of the operating point(s), methods of control and their effect on energy consumption.
System Curve
Based on these concepts, the total system head at any given flow rate is the sum of the static head and frictional head losses in the system. It, therefore, can be represented using the equation 1.A.7 (where the velocity at the supply and destination is negligible, e.g. they are tanks):
where:
- Δhsystem is system head, feet
- z is elevation, in feet
- p is pressure, in psi
- ρ is fluid density, in lbm/ft3
- 144 is to convert between square inches (in2) and square feet (ft2)
- f is friction factor
- L is pipe length, in feet
- D is pipe inside diameter, in feet
- v is average velocity in pipe, in ft/s
Note: Acceleration due to gravity is omitted in the pressure head portion of Eq. 1.A.7 due to units; therefore, it is only valid for standard earth acceleration due to gravity.
A system curve is a graphical representation of the relationship between flow rate and the associated static and frictional head losses. It is generated by calculating the static head and the frictional head losses at various flow rates and plotting them on a common set of axes.
Shape of the System Curve
In some systems the frictional losses will be the majority of overall head loss. These systems will have a steeper system curve.
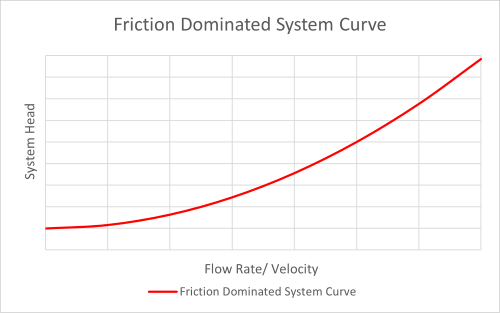
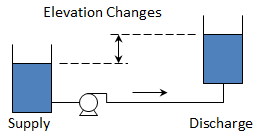
In other systems the elevation change, or static head, will be the majority of the overall head loss. The system curve in this case will start at a higher value at zero flow and will tend to be flatter.
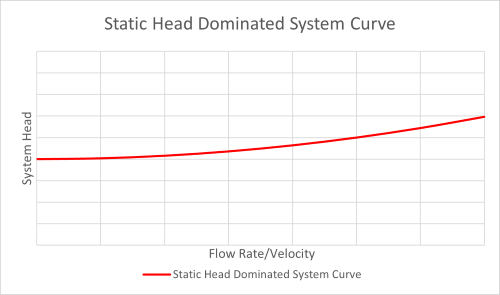
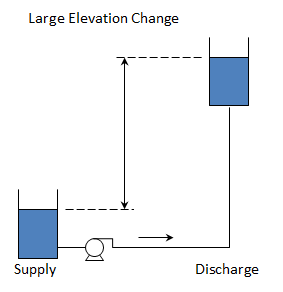
It is important to accurately characterize the system curve to select the correct pump for various operating conditions as the operating point of your system will be dependent on the intersection between the system curve and the pump curve.
System Curve Application
Real-world applications tend to consider a range or family of system curves. This would bracket the range of liquid levels, operating pressures, valve arrangements, etc.
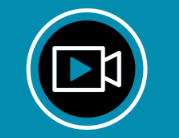
Vibration in Rotodynamic Pumps – Recorded Webinar
Learn basic vibration analysis concepts for rotodynamic pumps, the typical vibration issues that occur, with case studies to reinforce the concepts.
Educational Demonstration System Curve
This demonstrator shows qualitatively how various parameters affect the system curve. Slide the toggle to change system parameters and see how the system curve varies.
Use the red knobs to adjust the system parameters
Upper Tank Pressure
Lower Tank Level
Upper Tank Level
Friction Losses
(Major + Minor Losses)
Worked Example (U.S. & Metric Units)
Consider the system in Fig. 1.A.3 and develop a system curve for the flows from 0 to 300 GPM.
Determine the Static Head
Using the static head calculation in Eq. 1.A.3, and since both tanks have the same surface pressure, the static head is only dependent on the difference in surface elevation.
Determine the Pipe Friction and Properties
To simplify this example, we will consider the friction factor to be constant at 0.02. In general, the friction factor would vary as the flow rate (velocity) varies. Additionally, the flow would be laminar for low velocities. These considerations should be taken into account when calculating the pipe losses.
A 4-inch, schedule 40 steel pipe has an inner diameter of 4.026 inches (0.3355 feet). The overall pipe length in this example is 1255 feet.
Determine the Minor or Component Loss
The losses for the components can be found in tables. In this example we have the following:
- Regular flanged elbow (2), K = 0.31 each
- Swing check valve, K = 2.0
- Wedge-disc gate valve, K = 0.17
- Sudden enlargement, K = 1.0
This gives a total K factor equal to 3.79
Using the combined frictional loss equation in Eq. 1.A.7, we can determine the head loss in (feet)
Determine the System Curve
The system curve can be calculated by varying the flow rate (velocity) using the above values. Combining the static and frictional losses (pipe friction and minor losses) we have equation 1.A.8 describing system head as a function of static head and friction head, which the susequent calculations utilize to calculate system head as a function of velocity.
The following can be used to convert a flow rate (Q) in gpm (gallons per minute) to a velocity in ft/s (with the pipe diameter D in inches).
Substituting this in for velocity and using the 4-inch pipe (ID = 4.026 inches) we get the following as the system curve equation as a function of flow rate in gpm.
This, then, gives the following system curve data. This is a system that is dominated by the static head (there is a lift of 265 feet compared to little loss in piping and components).
System Curve Data
Flow Rate (gpm) | Velocity (ft/sec) | System Head (feet) |
---|---|---|
0 | 0 | 265 |
20 | 0.504 | 265 |
40 | 1.008 | 266 |
60 | 1.512 | 268 |
80 | 2.016 | 270 |
100 | 2.52 | 273 |
120 | 3.024 | 276 |
140 | 3.528 | 280 |
160 | 4.032 | 285 |
180 | 4.536 | 290 |
200 | 5.04 | 296 |
220 | 5.545 | 303 |
240 | 6.049 | 310 |
260 | 6.553 | 317 |
280 | 7.057 | 326 |
300 | 7.561 | 335 |
Last updated on July 19th, 2024